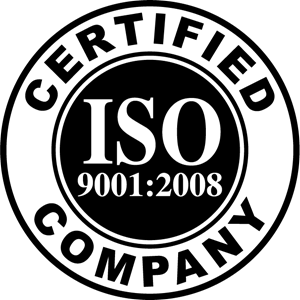
ISO 9001 definition: This is what the standard means?
Quality of product or service plays an overarching role in the success of a company. To ensure and maintain a high standard, many companies have introducedquality assurance systems. However, a quality management system is not only important for management. So that stakeholders and business partners can assess the effectiveness of the system, it is certified according to the ISO 9001 standard.
What is ISO 9001?
The importance of ISO 9001 arises from the high priority that quality management now has in the business world. With an appropriate system, companies try to maintain the quality of products and services at a high level in the long term.But this is not just of interest to management: a functioning quality management system is also important for investors, shareholders, and business partners. So that you can work with your company with confidence, and have your system examined and then certified by an independent testing agency.
With DIN EN ISO 9001 (the complete name of the standard) an international standard for checking quality management has been created. External service providers carry out an audit of the system and issue a certificate after passing the test. Important for the definition of DIN EN ISO 9001: The auditors do not check the quality of products or services, but rather test the system that is intended to ensure quality.
Advantages of ISO 9001
With ISO 9001 certification, companies can demonstrate to third parties that they have a good quality management system and thus guarantee sustainable success.
- Independent certification: An independent certificate is recommended so that third parties do not have to rely on your statements or even check each business partner themselves.
- International recognition: ISO 9001 is an international standard recognized around the world. This facilitates global collaboration and strengthens the company’s profile.
- Comprehensive review: The review by specialized auditors may reveal deficiencies. If you fix these, improved quality management will support your long-term success.
- Real trust: The ISO certificate builds trust in your company. This in turn simplifies work with (potential) business partners.
Who issues ISO 9001 certificates?
Independent testingorganizations are responsible for certification. DEKRA or the various regional TÜV organizations are certainly the best-known providers here. There are also other clubs and companies where you can book an audit.
The costs for certification depend primarily on how much time the testing center has to invest in the audit. Larger companies therefore usually pay more than small businesses. In addition, there are travel costs for the auditor. It may therefore be worthwhile to hire an examination center near the company headquarters. Many companies also take advantage of the opportunity to certify several systems in one audit. This also saves costs.
Requirements for the ISO standard 9001
To become certified, you first need a comprehensive quality management system that integrates the entire company. The test catalog is correspondingly extensive. Essentially, an audit looks at the following points:/p>
- Evaluation of the company: Document the most important key figures and facts about your company. In addition to internal factors such as the size of the workforce, this also includes external data on customers and market positioning. Part of the documentation also includes a list of the challenges that your quality management system must overcome.
- Management responsibilities: For the audit, it must be clear that upper management knows their responsibilities. Because this is where responsibility lies for the success of the quality assurance system. In addition, management should lead by example, live the established system, and communicate the goals of quality management openly and clearly.
- Planning the system: When planning your quality management system, it must be clear that you take into account all the risks that your company may encounter. ISO 9001 also requires you to define measurable goals.
- Involvement of personnel: ISO 9001 requires that the company’s workforce is actively involved in the quality assurance system. Above all, this requires sufficient communication from management.
- Provision of resources: For the system to function, appropriate resources such as infrastructure and budget must be released for it. But specialist knowledge must also be provided.
- Setting quality standards: To be able to measure whether your products have the desired quality, clear standards must also be set. This includes, for example, formulating construction plans in such a way that the desired standard can be achieved in a comprehensible manner.
- Contact with customers: Part of an ISO 9001 review also includes communication with customers. This includes, for example, customer support, which is an essential part of the offer and therefore also of product quality.
- Measuring quality: To ensure that the desired quality standard has been achieved and maintained, measurement concepts must be presented. The measurement instruments match the product or service.
- Optimizing the system: ISO 9001 requires that you continually develop your management system. React to problems and always look for opportunities for improvement.
The actual audit takes place in several steps. First, you should conduct an internal review. This serves as a test run and ensures that everything runs as smoothly as possible in the actual audit. For the external audit, you first submit the complete documentation. If the testing center is satisfied, the audit is carried out on-site, which also includes discussions with the employees.
An ISO 9001 certification is valid for three years. However, your company must undergo annual surveillance audits. These are less extensive and are intended to ensure that you continue to actively work on quality assurance.
Recommended article: Savouring the Season: Seasonal Fruits in India