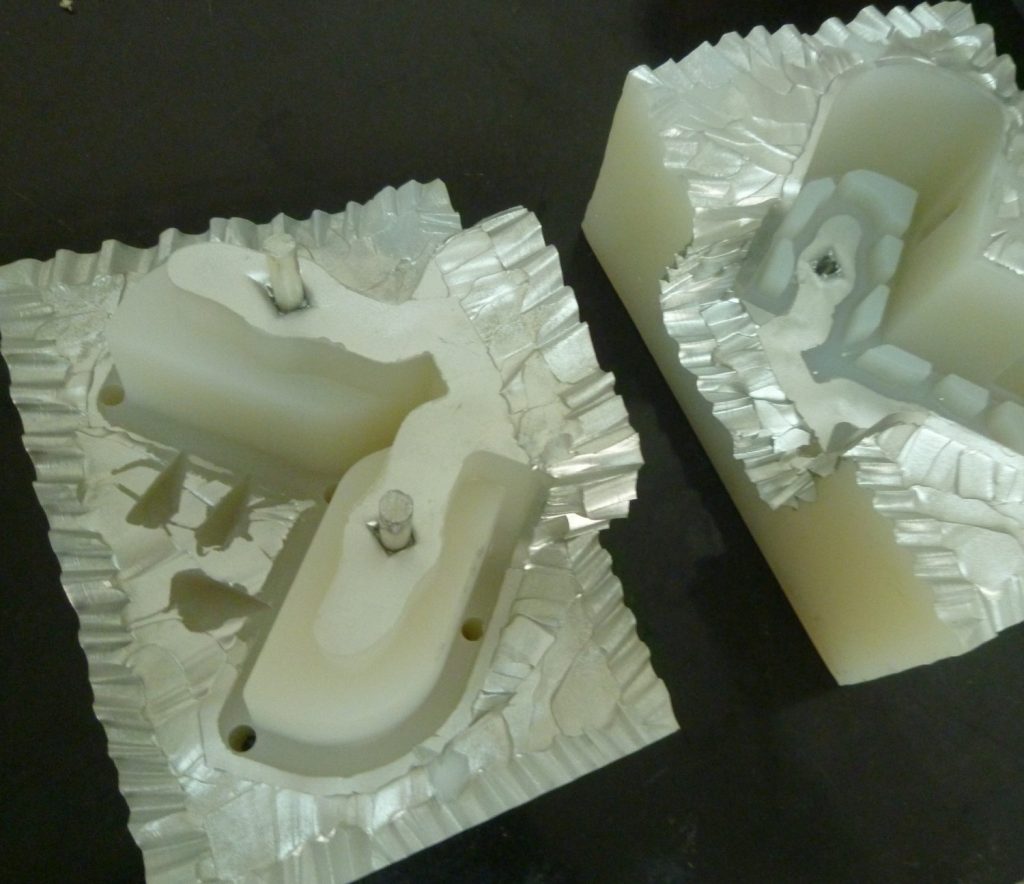
A Comparative Analysis of 3D Printed Prototyping and Vacuum Thermoforming
When choosing a method to build a model of a product, it’s important to consider established techniques like 3D printing and vacuum thermoforming. Both 3D printing a prototype and vacuum thermoforming are popular with product engineers and designers for different reasons. While 3D printing a prototype assists in design verification and testing and can be used for creating custom prototyping molds, vacuum thermoforming offers a different kind of flexibility. This guide compares these technologies to assist you in identifying the best approach for your project.
Thermoforming explained
Thermoforming involves heating a sheet of thermoplastic material to a pliable forming temperature. Once heated, it becomes easy to manipulate and stretch over a mold. After forming, the sheet cools down and retains the shape of the mold. Vacuum forming, a subset of thermoforming, is particularly effective in shaping the plastic sheet to the desired contour. Vacuum thermoforming is adaptable, allowing for the use of various materials to meet specific needs and purposes.
3D printing for prototyping
The process of 3D printing a prototype varies based on the application or purpose of the product. Current additive manufacturing technologies enable the customization of polymers through methods like multi-jet fusion (MJF), stereo lithography (SLA), and fused deposition modeling (FDM).
Although these methods differ in printing capabilities, technology, and materials, they generally follow a similar process. A digital design is processed using CAD software and then sliced into layers for the 3D printer. The printer then constructs the part layer by layer as per the instructions. Typically, the finished part undergoes post-processing, which may include support removal, painting, or sanding.
Choosing the right manufacturing technology
The decision between 3D printing a prototype and vacuum thermoforming should be based on the specific application and the volume of parts required. 3D printing is usually more cost-effective for producing a small number of parts. In contrast, vacuum thermoforming tends to be more economical for larger production scales. Note that thermoforming molds generally last for about 20 uses before needing replacement.
Vacuum thermoforming might be preferable for creating high-strength parts, as it uses two-component polyurethane resins that offer varied strength characteristics. However, if your project values design flexibility and aims to avoid expensive tooling or molding costs, 3D printing a prototype is the way to go.
Seeking expert advice?
HLH Prototypes offers expertise in both these technologies. For assistance in deciding between vacuum thermoforming and 3D printing a prototype, you can reach out to them for a free project review. Their team is ready to guide you in selecting the most suitable technology for your prototyping needs.
About the Company:
HLH Prototypes Co. Ltd is a company specializing in delivering tailor-made, fast prototyping and efficient low-volume production solutions. Situated in China, our prototyping firm ensures the speed and quality necessary for your project’s success. We extend our rapid part manufacturing services throughout China via our core offerings, which encompass sheet metal fabrication, CNC machining, swift tooling, rapid injection molding, urethane vacuum casting, FDM 3D printing, SLS 3D printing, and SLA rapid prototyping. We cater to a diverse clientele, including Fortune 500 corporations, small enterprises, and everyone in between, guaranteeing top-notch services. For additional details, please explore our website.