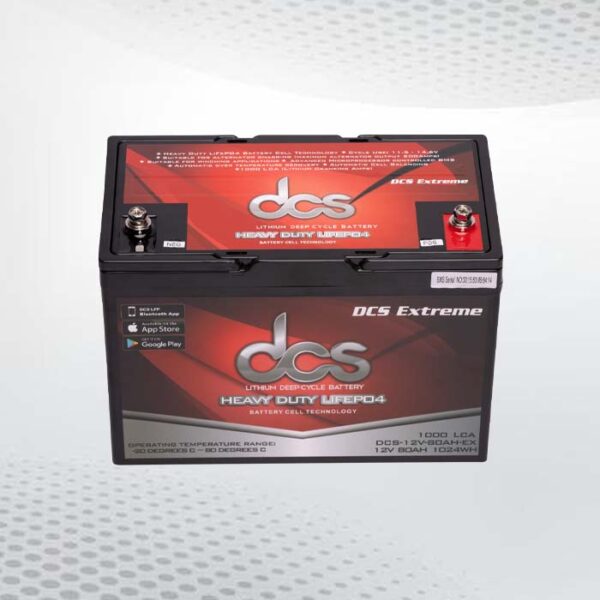
Inside Scoop on the Production Process of a 24v Lead Acid Battery
Are you curious how those powerful 24v lead acid batteries power trucks and other heavy-duty vehicles are made? You’re not alone! The manufacturing process of these essential energy sources may seem complex and mysterious, but we’re here to give you the inside scoop. In this blog post, we’ll take a closer look at the formula and production process of a 24v lead acid battery, giving you a better understanding of how they work and why they’re so reliable. So buckle up and get ready to dive into the fascinating world of battery production!
The Basics of a 24v Lead Acid Battery
Are you curious about the basics of a 24v lead acid battery? Well, let’s start from the beginning. These powerful energy sources are commonly used in trucks and heavy-duty vehicles. They provide the necessary power to start the engine, run various electrical systems, and even power accessories.
So, what makes a 24v lead acid battery tick? Let’s break it down. First, it consists of two 12v batteries connected in series, creating a 24v power supply. This arrangement allows for increased power and performance, perfect for the demands of trucks and other heavy-duty applications.
Inside the battery, there are several key components. The lead acid battery contains lead plates and sulfuric acid electrolytes. The lead plates, usually made of a lead alloy, are immersed in the electrolyte solution, facilitating the chemical reactions that generate electricity. This process involves the conversion of lead sulfate to lead dioxide and lead.
To ensure the battery functions optimally, it is important to maintain proper electrolyte levels, regularly check for signs of damage or corrosion, and keep the battery charged. Proper care and maintenance are essential for longevity and performance.
A Detailed Look into the Manufacturing Formula of a 24v Lead Acid Battery
If you’re eager to uncover the inner workings of a 24v lead acid battery and understand its manufacturing formula, you’re in the right place. This section will delve deeper into the production process and explore the key components of these powerful energy sources.
The manufacturing formula of a 24v lead acid battery involves careful selection and combination of materials to ensure optimal performance. The key ingredient in this formula is lead, which is used to create the plates inside the battery. Usually made of a lead alloy, these plates play a crucial role in generating electricity.
To enhance the battery’s performance, sulfuric acid electrolyte is added. This electrolyte acts as a conductor and facilitates the chemical reactions that convert lead sulfate into lead dioxide and lead, generating electrical energy.
The precise proportions and specific techniques used in the manufacturing process vary depending on the battery manufacturer. Factors such as plate thickness, plate design, and the type and concentration of electrolyte used all contribute to the battery’s overall performance and lifespan.
With an understanding of the manufacturing formula, you can now appreciate the intricate process of creating a reliable and efficient 24v lead acid battery. In the next section, we’ll explore special considerations in producing 24v truck batteries, so stay tuned!
Special Considerations in the Production of 24v Truck Battery
Several special considerations come into play when it comes to producing 24v truck battery. These heavy-duty vehicles have unique demands, and their batteries must be up to the task.
Firstly, the size and weight of the battery are important factors to consider. Trucks require larger and more powerful batteries than those used in smaller vehicles. This means that manufacturers must carefully design the battery to fit within the space constraints of the truck while still delivering the necessary power.
Additionally, the durability of the battery is crucial. Trucks often encounter rough terrains and extreme weather conditions, which can strain the battery. Therefore, special measures must be taken during the production process to ensure the battery can withstand these challenging environments.
Furthermore, the battery’s ability to start the engine quickly is essential for trucks. Truck drivers rely on their vehicles for their livelihoods, and any delay caused by a slow-starting battery can result in lost time and money. Manufacturers pay close attention to the design and construction of the battery to optimize its starting power and ensure reliable performance.
The Role of Quality Control in 24v Lead Acid Battery Manufacturing
Quality control plays a vital role in manufacturing 24v lead-acid batteries. It ensures that each battery meets strict performance, safety, and reliability standards. By implementing rigorous quality control measures, manufacturers can identify and rectify any issues during production, ensuring that only the highest-quality batteries reach the market.
One aspect of quality control in battery manufacturing involves testing the battery’s capacity and performance. This involves subjecting the batteries to various tests, such as checking their voltage output and verifying their ability to hold a charge. By conducting these tests, manufacturers can identify any batteries with defects or inconsistencies in their performance.
Another important aspect of quality control is ensuring the safety of the batteries. Manufacturers must carefully inspect each battery to meet safety standards and regulations. This includes checking for leaks, ensuring proper insulation, and verifying all connections are secure. Manufacturers can ensure that their batteries do not harm users or the environment by conducting thorough safety checks.
Additionally, quality control measures help manufacturers maintain consistency in the production process. By monitoring and controlling various factors such as temperature, humidity, and production techniques, manufacturers can ensure that each battery is produced to the same high standard. This consistency is crucial for the reliable performance and longevity of the batteries.
Sustainable Practices and Environmental Impact in Battery Manufacturing
Regarding battery manufacturing, sustainability and environmental impact are topics that cannot be ignored. As the demand for batteries grows, manufacturers must adopt sustainable practices and minimize their environmental footprint.
One key area of focus is the materials used in the manufacturing process. Many batteries contain heavy metals and toxic chemicals that can harm the environment if not handled properly. Manufacturers can take steps to reduce the use of these materials and find more environmentally-friendly alternatives. For example, they can explore using recycled materials or develop easier batteries to recycle at the end of their lifespan.
Energy consumption is another important consideration. Battery manufacturing requires significant energy, and using renewable energy sources can help reduce carbon emissions. Manufacturers can invest in solar or wind power or seek partnerships with renewable energy providers to ensure sustainable operations.
Additionally, waste management and recycling are crucial aspects of sustainable battery manufacturing. Manufacturers can implement proper waste management practices to minimize the amount of waste generated during production. They can also establish recycling programs to ensure used batteries are properly disposed of and recycled.
Optimizing Efficiency in the Production of 24v Lead Acid Batteries
To meet the demands of today’s fast-paced world, optimizing the Efficiency of battery production is crucial. Regarding 24v lead acid batteries, manufacturers are constantly looking for ways to improve their manufacturing processes and maximize Efficiency.
One key aspect of optimizing Efficiency is streamlining the production line. By analyzing and refining each manufacturing process step, manufacturers can identify areas where time and resources can be saved. This includes optimizing equipment usage, reducing waste, and minimizing production bottlenecks. By streamlining the production line, manufacturers can increase output and reduce costs, ultimately improving Efficiency.
Another strategy for optimizing Efficiency is implementing automation technologies. Automation can help streamline repetitive tasks, reduce human error, and increase production speed. By automating certain processes, manufacturers can free up valuable time and resources to focus on other aspects of production.
Furthermore, implementing lean manufacturing principles can also improve Efficiency. Lean manufacturing involves identifying and eliminating waste, whether in excess inventory, unnecessary transportation, or inefficient work processes. By eliminating waste and focusing on value-added activities, manufacturers can optimize Efficiency and improve overall productivity.
In addition to these strategies, collaboration and communication within the manufacturing team are essential. By fostering a culture of continuous improvement and open communication, manufacturers can encourage employees to share ideas and suggestions for increasing Efficiency. This collaboration can lead to innovative solutions and improvements in the production process.
Testing and Performance Analysis of 24v Lead Acid Batteries
Testing and performance analysis are essential to ensuring the quality and reliability of 24v lead acid batteries. These batteries undergo rigorous testing procedures to ensure they meet the necessary standards for performance and longevity.
Batteries are subjected to various assessments during the testing phase to evaluate their capacity, performance, and durability. This includes tests to check the battery’s voltage output, ability to hold a charge, and overall Efficiency. Manufacturers use specialized equipment and software to measure and analyze these factors accurately.
Performance analysis also involves assessing the battery’s ability to withstand different conditions and loads. This includes testing its resilience in extreme temperatures, vibration, and other demanding environments that trucks and heavy-duty vehicles may encounter. Manufacturers can identify any weaknesses or areas for improvement by simulating real-world scenarios.
Additionally, manufacturers conduct cycle testing to assess how the battery performs over time. This involves subjecting the battery to repeated charging and discharging cycles to evaluate its longevity and performance under regular use.
FAQs
You’ve made it to the FAQs section! We know you must have some burning questions about 24v lead acid batteries, so let’s dive in and provide some answers.
1. Are 24v lead acid batteries safe to use?
24v lead acid batteries are safe and reliable power sources when manufactured and used correctly. However, it’s important to handle them with care, follow proper charging and maintenance procedures, and avoid exposing them to extreme temperatures or conditions.
2. How long do 24v lead acid batteries typically last?
The lifespan of a 24v lead acid battery can vary depending on factors such as usage, maintenance, and environmental conditions. However, with proper care, these batteries can last anywhere from 3 to 5 years or even longer.
3. Can I use a regular charger to charge a 24v lead acid battery?
While it’s possible to charge a 24v lead acid battery with a regular charger, using a charger specifically designed for lead acid batteries is recommended. These chargers are optimized to deliver the correct voltage and charging profile, ensuring safe and efficient charging.
Conclusion
In this blog post, we’ve deeply explored the fascinating world of 24v lead acid battery production. We’ve explored the basics of these powerful energy sources, including their composition and how they work in trucks and heavy-duty vehicles. We’ve also delved into the manufacturing formula, highlighting the importance of lead and sulfuric acid electrolytes in generating electricity.