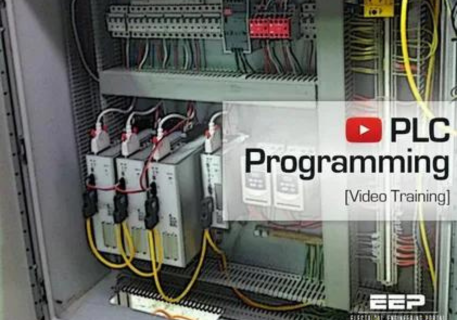
PLC Programming Course-Burraq Engineering Solutions
Understanding PLC programming
Programmable logic controllers (PLCs) have become indispensable in industrial automation, machine and process control in various sectors. At the heart of this automation is PLC programming, which allows engineers to create sequences of instructions that control the behavior of machines. In this comprehensive guide, Burraq Engineering Solutions delve into the basics of PLC programming course, its applications, and the key elements that make it a vital aspect of modern industrial control systems.
Basics of PLC programming
Definition and Functionality
A PLC is essentially a specialized digital computer designed to control industrial processes and machines. Unlike general purpose computers, PLCs are robust, reliable and adapted for real-time operation in an industrial environment. The primary function of a PLC is to read inputs, execute a program, and produce outputs based on the programmed logic.
Programming languages
PLC programming is usually done using ladder logic, which is a graphical programming language that resembles electrical relay logic diagrams. Other common programming languages include Function Block Diagram (FBD) and Structured Text (ST). Each language has its advantages, and the choice depends on the complexity of the control task and the preferences of the programmer.
PLC programming components
Inputs and Outputs (I/O)
PLCs interact with the physical world through input and output modules. Inputs, such as sensors and switches, provide data to the PLC, while outputs, such as actuators and relays, execute control commands. Understanding the connection between digital or analog signals from field devices and the PLC is key to effective programming.
Memory and data manipulation
PLCs have different types of memory, including input memory, output memory, and data memory. Programming involves managing data stored in memory, such as timers, counters, and variables. Correct data handling ensures accurate control and monitoring of industrial processes.
Operating instructions
PLC programs consist of a series of control instructions that determine the sequence of operations. These instructions include logic gates, timers, counters, and comparison functions. Skillful use of these instructions allows programmers to create complex control strategies that meet specific process requirements.
Application for PLC programming
Automation of production
PLCs play a key role in manufacturing automation by controlling processes such as assembly lines, packaging and quality control. With the ability to program complex sequences and adapt to changing production requirements, PLCs are indispensable in modern manufacturing environments.
Process control
In industries such as chemical processing and power generation, PLCs regulate complex processes to ensure optimal performance and safety. PID (Proportional-Integral-Derivative) control loops implemented through PLC programming help maintain precise control over variables such as temperature, pressure and flow.
Building automation
PLCs are widely used in building automation systems to control HVAC (heating, ventilation and air conditioning), lighting and security systems. The flexibility of PLC programming enables the implementation of energy-efficient strategies and the seamless integration of various building subsystems.
Programming tools and PLC development
Programming software
PLC programming is facilitated by specialized software supplied by manufacturers. These tools offer a user-friendly interface for creating, editing and debugging PLC programs. Knowledge of programming software is essential to effectively translate control requirements into functional code.
Simulation and testing
Before deploying PLC programs to control real processes, engineers often use simulation tools to verify and test the logic. Simulation helps identify potential problems and ensures the reliability of the control strategy, thereby reducing the risk of errors in real-world applications.
Conclusion
PLC programming is a critical aspect of industrial automation and enables engineers to create intelligent control systems for a wide variety of applications. From the basics of ladder logic to the intricacies of control instructions, a good understanding of PLC programming is essential for industry professionals. As industries continue to evolve, the role of PLCs and their programming will become more important to the advancement of automation and efficiency in manufacturing and beyond.