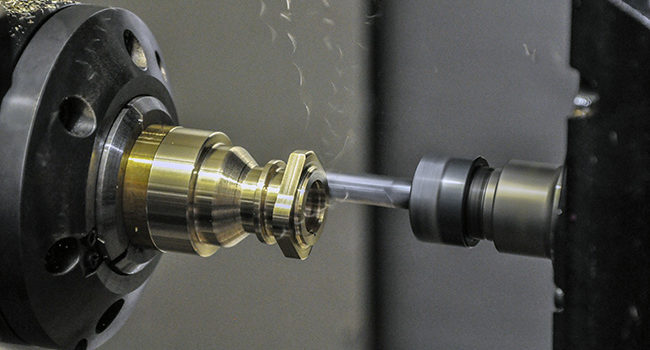
Revolutionizing Precision Engineering: Unveiling the Power of Milling Machine Universal and Turn Mill Machine
In the world of precision engineering, the choice of machinery plays a pivotal role in shaping the efficiency and versatility of manufacturing processes. Two key players that have transformed the landscape are the milling machine universal and the turn mill machine. In this comprehensive guide, we delve into the intricacies of these cutting-edge tools, exploring their features, applications, and the distinct advantages they bring to the realm of machining.
Milling Machine Universal: Unleashing Precision and Versatility
-
Understanding the Basics:
The milling machine universal is a versatile machining tool that stands as a cornerstone in the world of metalworking. It operates with rotary cutters to remove material from a workpiece, allowing for a wide range of intricate shapes and details. Unlike its counterparts, the universal milling machine features a swiveling table that can be adjusted to various angles, providing unparalleled flexibility in machining operations.
-
Versatility in Action:
One of the standout features of the milling machine universal is its ability to handle both horizontal and vertical milling tasks with equal efficiency. This dual capability allows manufacturers to execute a diverse array of milling operations, from simple slotting and keyway cutting to complex contouring and 3D profiling. The universal milling machine’s adaptability makes it an indispensable tool in industries ranging from aerospace to automotive.
-
Precision Redefined:
Precision is the hallmark of any exceptional machining process, and the milling machine universal excels in this aspect. The combination of a robust structure, advanced control systems, and high-quality cutting tools enables this machine to achieve tight tolerances and impeccable surface finishes. Manufacturers can rely on the universal milling machine to meet the exacting standards demanded by modern engineering applications.
-
Applications Across Industries:
The universal milling machine finds application in a myriad of industries, including manufacturing, tool and die making, and prototype development. Its ability to switch between various cutting orientations makes it an ideal choice for producing components with intricate geometries. From creating molds for injection molding to crafting precision components for the medical field, the universal milling machine proves its worth across diverse sectors.
Turn Mill Machine: Seamlessly Integrating Turning and Milling
-
A Fusion of Capabilities:
The turn mill machine represents a revolutionary approach to machining by seamlessly integrating turning and milling functions into a single, efficient unit. This innovative design eliminates the need for multiple setups and tool changes, streamlining the manufacturing process and significantly reducing production times. The turn mill machine is a true multitasker, capable of handling complex workpieces with unparalleled precision.
-
Efficiency Unleashed:
Traditional manufacturing processes often involve separate machines for turning and milling, leading to increased production times and higher costs. The turn mill machine eliminates these inefficiencies by performing both operations in a single setup. This not only accelerates the production cycle but also enhances overall accuracy, as the workpiece remains undisturbed throughout the entire process.
-
Complex Geometries Made Simple:
One of the standout advantages of the turn mill machine is its ability to tackle complex geometries with ease. Whether it’s the creation of intricate components for the aerospace industry or the production of medical implants with precise specifications, the turn mill machine’s multitasking capabilities open up new possibilities for engineers and manufacturers.
-
Enhanced Precision through Integration:
Integrating turning and milling functions within a single machine not only boosts efficiency but also enhances overall precision. The turn mill machine’s synchronized movements and advanced control systems ensure that every aspect of the machining process is executed with the utmost accuracy. This level of precision is crucial in industries where component quality is non-negotiable.
Choosing the Right Machine for Your Needs:
-
Consideration of Workpiece Complexity:
When deciding between a milling machine universal and a turn mill machine, consider the complexity of your workpieces. If your projects involve intricate geometries and a mix of turning and milling operations, the turn mill machine may be the ideal choice. For more straightforward milling tasks with the need for flexibility, the milling machine universal is a solid option.
-
Production Volume and Efficiency:
Assess your production volume and efficiency requirements. The turn mill machine’s ability to perform multiple operations in a single setup can significantly reduce production times, making it suitable for high-volume manufacturing. The milling machine universal, while versatile, may require more setup changes for certain operations.
-
Budget Considerations:
Budget constraints often play a crucial role in the decision-making process. While both machines offer unparalleled capabilities, the turn mill machine’s integrated design may come with a higher initial cost. Evaluate the long-term cost benefits in terms of increased efficiency and reduced production times.
Conclusion:
In the dynamic landscape of precision engineering, the choice between a milling machine universal and a turn mill machine is a decision that shapes the efficiency and capabilities of a manufacturing process. Both machines bring unique advantages to the table, from the universal milling machine’s versatility to the turn mill machine’s seamless integration of turning and milling functions.
Ultimately, the decision should align with the specific needs of your projects, considering factors such as workpiece complexity, production volume, and budget constraints. Whichever path you choose, embracing these advanced machining technologies is a step toward revolutionizing your manufacturing processes and staying ahead in the ever-evolving world of precision engineering.