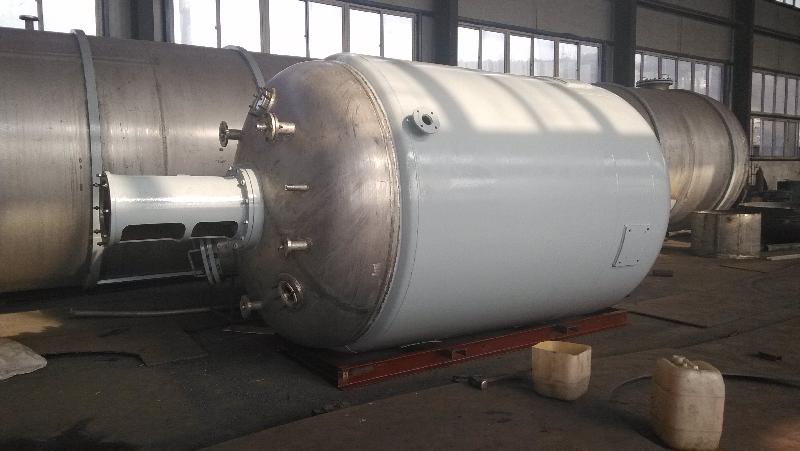
How to Design and Select a Reactor for Sustainable Production?
Chemical reactors are the heart of any manufacturing process. Choosing and designing a reactor is one of the most challenging parts of being a chemical engineer. However, there are some simple steps to follow that will make the design process much easier.
Pharmaceutical production is moving away from outdated batch processes to continuous reactions. These processes offer a number of benefits, including lower costs and improved product quality.
Reactors for sale
Using a reactor for sustainable production can help meet energy demand while reducing anthropogenic carbon dioxide emissions associated with power generation. It can also provide process heat for desalination and other industrial applications. This guide outlines the benefits of these systems and demonstrates how to evaluate designs and choose a suitable reactor for a project.
A number of nuclear reactor designs are currently under development for the next generation of power plants. These reactors are designed to be more efficient, flexible, and environmentally friendly than existing reactors. They are being developed by an international task force that is sharing R&D and developing multinational regulatory standards. The task force is working on six Generation IV reactor technologies, including four fast neutron reactors for hydrogen production.
These include the USA’s SSTAR and Japan’s LSMR. The LSMR’s lead-bismuth cooling system draws on 80 years of experience with this technology in submarine reactors. It also aims to reduce fuel costs by operating at lower power factors and using epithermal rather than fast neutrons.
The European Union’s ALFRED technology demonstrator is another LFR design. It is expected to be built in the 2020s and will operate on mixed oxide (MOX) fuel, with up to 17% plutonium and recyclable minor actinides. It will also use molten lead to produce steam for power generation.
Used reactors
The design and selection of a reactor is an important part of chemical engineering. It is essential to consider the reaction kinetics and desired product purity. The reactor should also be able to operate at the required temperature and pressure. In addition, it should be able to provide sufficient cooling and oxygen. This ensures that the reaction takes place at a controlled rate. This will help prevent reactions from becoming unstable and produce unfavorable side-products. In addition, the reactor should be resistant to contamination and corrosion.
Used reactors can be an economical solution for many chemical processing applications. These vessels can be bought and sold at online auctions or from a broker. Some sellers have a variety of sizes and styles available. In addition, used reactors are often refurbished or repaired to improve efficiency and safety. This can significantly reduce operating costs.
Aside from the cost savings, there are other benefits of using a used reactor. For example, used reactors are ideal for processes that require high throughput. They can also be used to store chemicals or reagents. In addition, these reactors are more durable than newer units.
In a Bisconti-Roper survey, 79% of those surveyed supported recycling used nuclear fuel (contrary to past US policy) and 83% supported centralized storage sites until a permanent disposal facility is ready. This could be an excellent option for meeting the future energy demands of a growing global population while reducing anthropogenic carbon dioxide emissions.
Chemical reactors
Chemical reactors are a vital part of any manufacturing process that requires a chemical change. They can be used for a variety of applications, including production of pharmaceuticals and other chemicals. The design of a chemical reactor depends on several factors, including reaction kinetics, enthalpy of the reaction, and heat and mass transfer. In addition, the method of product separation impacts the reactor design. The physical operations that occur in a reactor are also important considerations, as they can cause hazards like explosions and leaks.
The use of continuous flow chemistry in industrial processes is increasing rapidly. The technology offers many benefits, such as improved safety, increased efficiency, and reduced waste. However, the challenge is to scale up this technology from laboratory to plant-scale processing. In order to achieve this, the process needs to be redesigned and optimized to produce target yields and selectivities. buy reactors from the best reputable seller surplusrecord.
The Emanuelsson research group has developed a device that mimics the action of a record player and allows enzymes to be placed on woolen cloth discs, where they can react with a chemical substrate without being sheared or denatured. The technique has potential to be a cost-effective solution for pharmaceutical intermediaries, which need to source their APIs from companies that can deliver them more quickly and sustainably. It can also provide a pathway for local production of essential chemicals and drugs, which would reduce the need to rely on global supply chains during crises such as the coronavirus pandemic.
Reactor design
The design of a reactor for sustainable production must be considered carefully to ensure its safety. It must be capable of withstanding accidents, such as explosions and fires. It must also be able to withstand the heat generated by the reaction. In addition, it must be designed to avoid contamination and allow the removal of impurities. The pebble-bed reactor, a high-temperature gas-cooled reactor (HTGCR) that uses ceramic fuels, meets these requirements. It is cooled by inert helium rather than water, which prevents steam explosions and resists neutron absorption that can lead to radioactivity. The helium also prevents the formation of a radioactive oxide film on the surface of the uranium nuclei. The helium is also safer because it does not absorb water and cannot melt contaminants.
Several factors determine the design of a continuous reactor, including reaction kinetics, enthalpy of reaction, and heat and mass transfer. A good continuous reactor design must consider these factors in order to achieve a high level of efficiency.
Ideally, the reactor will have perfect radial mixing and uniform temperature and concentration throughout its length. However, this is not always possible in practice. For this reason, continuous reactors are typically used for industrial processes, such as in the pharmaceutical industry. Continuous reactors are also widely used in continuous processes such as fermentation and biochemical reactions. Reactors can be used as line or load reactors. The former are used when low line impedance allows high inrush current, while the latter is installed at the output of a motor drive. A load reactor can help eliminate voltage spikes and reduce harmonic distortion in the output waveform of a motor drive.