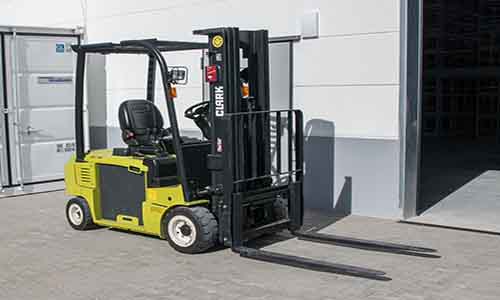
Forklift Train the Trainer and WHMIS Training: Empowering Workplace Safety
Workplace safety is a top priority for employers across various industries. Ensuring that employees are well-trained in handling potentially hazardous situations is crucial for preventing accidents and injuries. Two key aspects of workplace safety training are Forklift Train the Trainer programs and WHMIS Training. In this article, we will explore the significance of these training programs and how they empower individuals and organizations to create safer work environments.
Forklift Train the Trainer: Shaping Competent Instructors
Forklifts are a common sight in warehouses, construction sites, and manufacturing facilities. These powerful machines simplify the movement of heavy materials, but they also pose significant risks if not operated correctly. Forklift accidents can result in serious injuries or even fatalities. Therefore, it’s essential to have qualified forklift instructors who can provide comprehensive training to operators. This is where Forklift Train the Trainer programs come into play.
The Role of a Forklift Trainer
A forklift trainer is responsible for teaching individuals how to operate forklifts safely and efficiently. Their role includes:
- Instructing New Operators: Providing hands-on training to new forklift operators, covering topics such as machine controls, stability, load handling, and safety procedures.
- Reinforcing Safety Protocols: Ensuring that operators understand and follow safety guidelines to prevent accidents, such as keeping a safe distance from edges and load capacities.
- Conducting Regular Evaluations: Assessing the skills and knowledge of forklift operators through practical tests and written examinations to ensure ongoing competence.
- Staying Informed: Keeping up with the latest industry standards and safety regulations to update training materials and methods as needed.
Forklift Train the Trainer Programs: Key Benefits
- Internal Expertise: Developing in-house forklift trainers through Forklift Train the Trainer programs allows organizations to have experts who understand the specific needs and challenges of their workplace.
- Cost-Effective: Training in-house trainers can be more cost-effective in the long run compared to outsourcing training to external providers.
- Customization: Organizations can tailor their forklift training programs to suit their unique operational requirements and safety protocols.
- Consistency: Internal trainers ensure a consistent and standardized approach to forklift training throughout the organization.
- Adaptability: Trainers can quickly respond to changes in safety regulations and adapt training materials accordingly.
The Process of Becoming a Certified Forklift Trainer
To become a certified forklift trainer, individuals typically follow these steps:
- Choose a Training Program: Select a reputable Forklift Train the Trainer program that aligns with industry standards and safety regulations.
- Complete the Training: Engage with the course materials, which include instructional content, teaching techniques, and assessments. Gain expertise in forklift safety, operation, and training methodologies.
- Pass the Trainer Evaluation: Many programs require participants to undergo an evaluation to assess their ability to effectively teach forklift operation and safety.
- Obtain Certification: Successful completion of the program and evaluation results in certification as a forklift trainer, allowing individuals to provide training within their organization.
- Continuous Learning: Stay up-to-date with evolving safety standards and best practices by participating in ongoing professional development.
WHMIS Training: Hazardous Materials Knowledge is Power
In addition to forklift training, another critical component of workplace safety is WHMIS (Workplace Hazardous Materials Information System) training. WHMIS is a comprehensive system designed to provide information on hazardous materials used in the workplace. The goal is to ensure that employees understand the risks associated with these materials and know how to handle them safely.
The Importance of WHMIS Training
WHMIS training plays a vital role in preventing accidents, chemical exposures, and illnesses caused by hazardous materials in the workplace. Here’s why it’s essential:
- Risk Awareness: WHMIS training educates employees about the potential hazards of chemicals they work with, empowering them to make informed decisions.
- Safety Protocols: Employees learn about the proper storage, handling, and disposal of hazardous materials, reducing the risk of accidents and environmental harm.
- Emergency Response: WHMIS training includes information on how to respond to chemical emergencies, minimizing the impact of accidents.
- Regulatory Compliance: Compliance with WHMIS regulations is often a legal requirement in many industries, and failure to do so can result in penalties.
- Protection of Health: By understanding the risks and using appropriate protective measures, employees can safeguard their health while working with hazardous materials.
WHMIS Training Programs: Key Benefits
- Legal Compliance: WHMIS training ensures organizations comply with legal obligations to provide safety information to employees.
- Risk Reduction: Educated employees are less likely to mishandle hazardous materials, reducing the risk of accidents and injuries.
- Health Protection: WHMIS training contributes to the well-being of employees by helping them understand and minimize the health risks associated with their work.
- Environmental Responsibility: Proper handling and disposal of hazardous materials protect the environment from contamination.
- Increased Confidence: Employees who receive WHMIS training feel more confident in their ability to work safely with hazardous materials.
The WHMIS Training Process
The process of WHMIS training typically involves the following steps:
- Identify Hazardous Materials: Determine which hazardous materials are present in the workplace and create an inventory.
- Select a Training Program: Choose a WHMIS training program that aligns with the specific hazards and chemicals in the workplace.
- Deliver Training: Provide employees with access to WHMIS training materials, which may include online courses, in-person sessions, or a combination of both.
- Assess Understanding: Evaluate employees’ understanding of WHMIS through assessments and quizzes.
- Certify Completion: Provide certification or documentation to employees who successfully complete the WHMIS training.
- Regular Updates: Ensure that employees receive refresher training as needed and when new hazardous materials are introduced.
Conclusion
Workplace safety is a shared responsibility, and training plays a pivotal role in creating a secure working environment. Forklift Train the Trainer programs empower individuals to become competent instructors who can guide forklift operators safely and effectively. Meanwhile, WHMIS Training equips employees with the knowledge needed to handle hazardous materials responsibly. Together, these training programs contribute to safer workplaces, reduced accidents, and a healthier workforce. Organizations that invest in these training initiatives not only meet legal requirements but also foster a culture of safety and well-being.