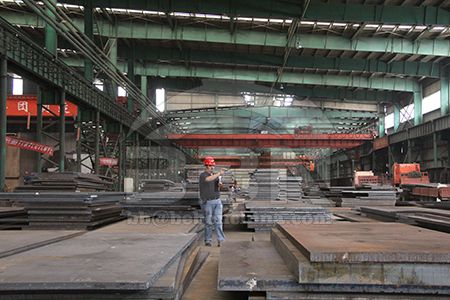
A Guide To Understanding Wear Plates And Their Significance
Wear plates play a crucial role in industries that require heavy equipment usage, such as mining, construction, and manufacturing. Despite their essential purpose, many people are unfamiliar with what wear plates are and how they contribute to a machine’s performance and longevity. There are many wear plate exporters but this guide aims to provide a comprehensive understanding of wear plates and their significance in various industries.
What are Wear Plates?
Wear plates, also known as abrasion-resistant plates or liners, are protective sheets made from high-quality materials like steel or aluminum. They are designed to fit onto surfaces subjected to wear, creating a barrier against abrasion, corrosion, impact, and other forms of damage. These plates prevent the underlying machinery from deteriorating due to repeated friction or impact, ensuring better performance and extending the equipment’s lifespan.
Significance of Wear Plates
1. Protection against Wear and Tear:
Heavy-duty machinery often experiences intense wear and tear due to the nature of its usage. Wear plates act as a protective shield, minimizing the damage caused by frequent contact with abrasive materials, rocks, or heavy loads. By reducing wear and tear, wear plates help maintain the integrity and efficiency of the machinery.
2. Improved Equipment Performance:
When machines suffer from excessive wear, their performance and efficiency decline. Wear plates ensure smooth operation by reducing friction and impact, preventing downtime and costly repairs. By maintaining proper equipment functionality, these plates contribute to improved productivity and increased profitability in various industries.
3. Extended Equipment Lifespan:
By reducing the damage caused by wear and tear, wear plates significantly extend the lifespan of heavy machinery. They protect critical components, such as buckets, blades, chutes, and hoppers, which are prone to damage due to constant use and exposure to harsh materials. Extending equipment lifespan not only saves money on replacements but also minimizes the downtime required for repairs.
4. Cost-Effective Solution:
Investing in wear plates may seem like an added expense initially, but it proves to be a cost-effective solution in the long run. By protecting machinery, wear plates reduce maintenance and repair costs. Additionally, the extended equipment lifespan reduces the frequency of replacements. Consequently, businesses can allocate their resources towards other essential areas, contributing to overall profitability.
Choosing the Right Wear Plate
Selecting the appropriate wear plate is crucial to ensure optimal protection and performance. Here are some factors to consider:
1. Material:
Wear plates are available in various materials, such as steel, chrome carbide, or ceramic, each with its own unique properties and levels of resistance. The choice depends on the application, type of wear, and environmental conditions.
2. Thickness:
The thickness of the wear plate should be determined based on the severity of wear and impact expected. A thicker plate can withstand high levels of damage, while a thinner plate may be sufficient for less demanding applications.
3. Installation Method:
Different wear plates require specific installation methods. Some can be welded, bolted, or glued onto the surface. Considering the machinery and maintenance requirements, choose the most suitable method.
Conclusion
Understanding wear plates and their significance in heavy-duty industries is crucial for improving equipment performance, reducing maintenance costs, and extending machinery lifespan. By investing in the right wear plates and ensuring proper installation, businesses can protect their valuable machinery and drive productivity and profitability.